2021 W&H Complete Paper Sack Line
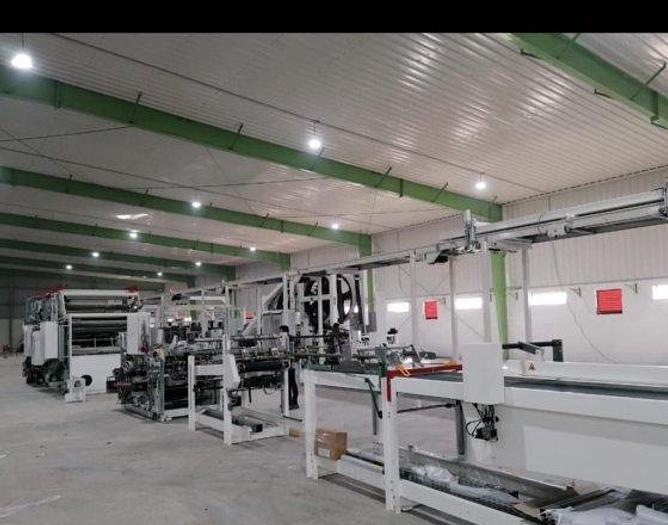
2021 W&H Complete Paper Sack Line
Available quantity:1
Description
W&H Complete Multiwall paper sack line year 2021 is equipped with tuber AM 8115, 3 plies, stepped end and flush cut, inline printer Flexo 820 with web width of 1370mm, bottomer AD 8320 CL with valve unit for the production of cement sacks of 2 or 3 plies.
Complete paper sack lines, Industrial sack lines, bottom patch Bottomer AD 8320 Cl, Cement sacks, Flush cut, stepped end, Transystem, Tuber AM 8115, W&H, Windmöller&Holscher, With valve unit, year 2021
W&H complete paper sack line year 2021
Tail End Printer
Brand: W&H
Model: FLEXA 820
Web width: 1370mm
Printing width: 1320mm
Print repeat range: 450–1500mm
4 doctor blade printing decks
Ceramic coated anilox roll 140 lines/cm
Manual lateral register adjustment : +/- 5mm
Output speed when equipped with doctor chamber inking system: 350 m/min, depending on job specification and print related factors, such as vibrational response of the colour deck (bouncing) due to cross bar designs
Note: because of the high printing speeds, the use of print cylinders with integral journals is recommended. When printing special designs, in particular cross bar designs, limitations to the print quality or limitations to the resulting machine speed have to be expected!
Materials to be printed: paper 40–250gsm
Inks: water based
Tuber W&H
Model: AM 8115
3 plies
Stepped end and flush cut
Web guide system
Web threading belts for each ply
Web draw assemblies with automatic web tension control to adjust web tension for each individual ply in the web processing section
Stepped and cross perforation
Cross pasting
Register rollers, seam pasting, tube forming section, flush cut unit, belt tear-off unit, packet forming station, hardware accessories for remote service, 3 automatic transverse realigning of material rolls, end -printer integration parts for the unwind, tension control system with 4Q drive, ionization unit, mobile paste pump station (50 liters), brush roller for stepped end cross perforation, register unit for intermediate PE ply, automatic position control of flush cut unit, all-over venthole perforation, quick change system for seam and cross paste units, panless glue units for cross pasting, nonstick coating of idler rollers in the cross pasting station, easy stop function, automatic lubrification system at the cross pasting station
Min-max flat tube width (depending on equipment specification): 180 – 750 mm
Min-max cut-off length, stepped end (depending on equipment specification): 380 – 1500 mm
Min-max cut-off length, flush cut (depending on equipment specification): 320 – 1650 mm
Max roll width: 1530 mm
Max roll diameter: 1300 mm
Max. output: 500 tubes/min (max speed for cut-off lengths up to 75cm (double-tool range): 500 tubes/min; max speed for cut off lengths of 76cm and above (single-tool range): 350 tubes/min)
Weight (depending on machine specification; actual dimensions per machine related installation drawing): without paper, without printer: approx. 34.000kg
Connected load: without printer approx. 90kva, with printer approx. 105kva
Automation TRANSSYSTEMS 1
Standard equipment of Automation TRANSYSTEMS including:
Conveyor for transport of packets in the longitudinal direction 1,80 m
Press plate for 1 packet
Conveyor for transport of packets in the longitudinal direction 2,90 m
Corner roller conveyor to redirect tube packets for right handled onward transportation
Turnover station for transport of packets in the cross direction to turn tube packets about their longitudinal axis
Supporting frame for two automation elements
Collating conveyor for transport of packets in the transverse direction length: 5 m, to collect closely to each other a preselected number of packets
Storage conveyor (s) for transport of packets in the transverse direction length: 5,00 m, for automatic storing of packet groups
Press plate without guard for storage conveyor, pneumatically actuated
Storage conveyors for transport of packets in the transverse direction length: 5,00 m, for automatic storing of packet groups
Traversing unit for a storage conveyor, to transfer a group of packets in case of laterally offset storage conveyors
Demand conveyor for transport of packets in the transverse direction length: 5 m
Auto loader type “M” for automatic loading of the rotary feeder with tube packets
AUTOMATED MATERIAL FLOW SYSTEM between Tuber AM 8115 and Bottomer
Min-max tube width: 280–600mm
Min-max tube length: 440–1050mm
Bottomer W&H
Model: AD 8320 CL
for 2 and 3 plies cement sacks
With valve unit
Min-max sack lengths stepped end: 320–740mm
Min-max sack lengths flush cut: 320–740mm
Min-max bottom widths stepped end: 80–140mm
Min-max bottom widths flush cut: 80–140mm
Min-max sack width: 280–550mm
Min-max width of opened bottom: 160–340mm
Min-max bottom center: 240–700mm
Tube lengths: 400–940mm
Valve unit:
Unwind with air shaft for a max. roll diameter of 1300 mm and 76 mm inner core diameter
Package to run 2-ply valves
PE film perforating tools at the valve unit
Controls systems: VCS 2 opto electronic device for automatic detection of missing and/or misplaced valves
Valve patch:
Min-max cut-off length: 100–250mm
Min-max valve length: 100–240mm
Min-max fold over length: 0–120mm
Min-max roll width: 100–300mm
Bottom patch:
Min-max cut-off length: 160–450mm
Min-max web width: 80–180mm
Paste pad thickness (can be guaranteed only when photopolymer plates are used): 4.7mm
Recommended printing plate thickness (including compressible base of 0.3–0.5mm. Different plate thickness on request, however not less than 3.14 mm): 3.14mm
CCS expansion for include checking of leading and trailing edge bottom slits, pair of opto-electronic sensors to scan the bottom edges
PCS print control system for automatic registering of bottom patch print in relation to the cut
1x flexo bottom patch printer for one colour for printing of two bottom patch webs side by side on one cylinder with web guide
1x flexo bottom patch printer for second colour configured exactly the same as the one colour patch printer without web guide
Max. output: the output achievable under field conditions is dependent on product design and dimensions as well as on compliance with material and environmental properties: 360 sacks/min
Pressing and packet forming station: 33 packets/min, without metal detector
Min. sack count per packet: 10 sacks
Max. packet height: 150mm
Dimensions of machine: as per layout drawing
Power consumption: as per layout drawing
Voltage rating, in case of different power/mains characteristics, a series transformer is required: 3 x 400v with neutral
Glue preparation plant
Slitter rewinder: Longslit 1013P
Working width: 1350mm
Max unwinding roll diameter: 1300mm
Max inner core diameter: 76mm
Rewinding roll diameter: 1300mm
Inner core diameter: 76mm
Slitting width: min. 25mm with max. 30 knives
Material: paper 50–200g/m²
Max speed: 400m/min (depending on material)
Drive: A.C. 3 phases motor KW 30
Operating and display system via touch panel
Power supply: 400V, 50Hz, 35kv
Immediately available
Can be seen in production
Specifications
Manufacturer | W&H |
Model | Complete Paper Sack Line |
Year | 2021 |
Condition | Used |
Stock Number | 58147 |